I commend you for your commitment to your product and your customers. I have never regretted getting an AC system after talking to you. Many friends run their 12 volt units for several hours to fill the tank, while monitoring/augmenting battery amps. That is a lot of wear on the components for a little water. I never run mine for more than an hour, getting the amps from the main engine, my Honda generator, or shorepower. I have made more than 1000 gallons of water so far, with only 37 hours of run time.
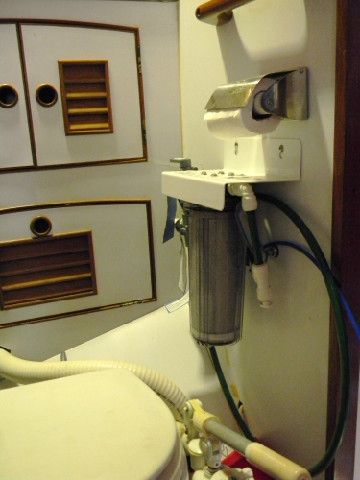
Lane Scott
Rich and Charlie use industry standard parts, know what they’re doing, and don’t try to rip you off on the price. The new membranes fit exactly where the old ones were and with the new vessel, metal end caps, and two new hoses there are no leaks! A first for our system. And with the true 40″ membranes we’re getting 40 gallons per hour water production. An increase of 8 gallons per hour over the old system.
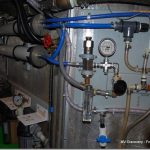
Frank & Linda
The water maker installation was pretty much by the book, and questions were quickly resolved by the Cruise RO Water team. The water production rate is beyond the advertised value and the water quality seems excellent. The system is simple and straight forward to operate and maintain. The system’s simplicity augments its reliability and serviceability affording good purchase price value.
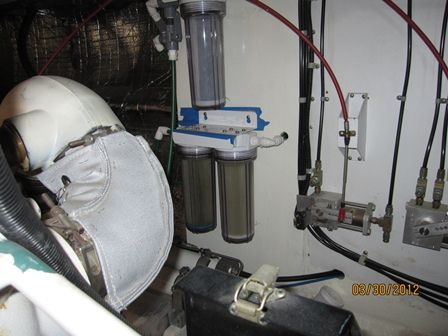
Marvin Sachse
After a few years of cruising with a low output 12v DC water maker, Mark decided it was time to upgrade to a 120v AC high output water and chose our SM30. Not only is our 30 gallon per hour water maker less expensive than a 8 GPH 12v DC water maker to purchase, now you can make water every few days rather than needing to make water daily to keep up with showers and a more comfortable level of water usage that as we say, “lets you go Cruising rather than Camping”
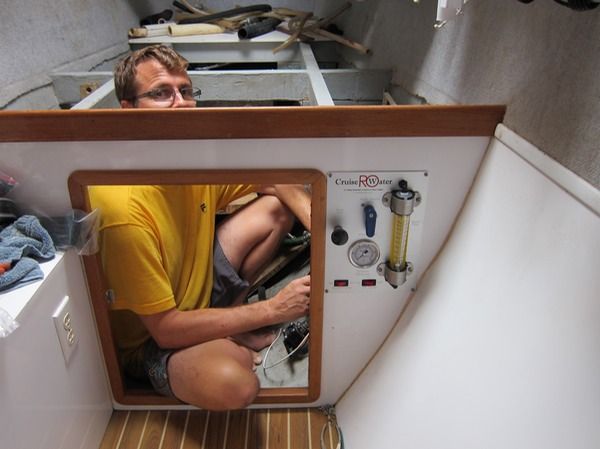
Mike & Michele